
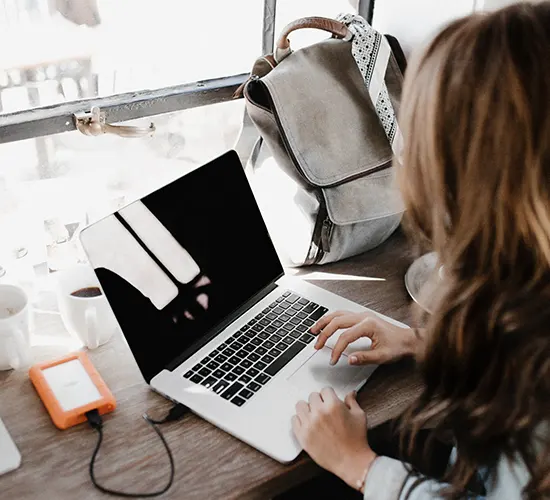
Google Search

A well-documented Business Plan aids in business funding and it is proven to help businesses grow by 30% faster.

Test Your Business ideas- We clear your doubts on Business concept and validate it properly. Often Businesses fail when the Business Plan is weak.

Market Research & High Industry Demand- We will analyse the Market Potential for optimal Industry Growth.
- Overview
- Stats
- Introduction
- Information
- Contact Us
- Project At A Glance
- Profitability And Net Cash Accruals
- Cost Of Project
- Asssessement Of Working Capital Requirements
- Profitability Ratios, Dscr, Debt Equity
- Break Even Analysis
- Means Of Finance
- Projected Balance Sheet
- Repayment Of Term Loan
- Debt Service Coverage Ratio
- Depreciation Chart
- Projected Pay-Back Period
- Projected Irr
- Company Summary
- Reasons For Buying The Report
- Our Approach
- Table Of Content
- Financial Plan
- Information/ Disclaimer
Setup Unit Of Compressed Bio Gas Using Napier Grass
Compressed Bio Gas provides a significant step forward in the search for renewable energy alternatives, with Napier Grass emerging as an attractive feedstock. This tropical perennial, with its quick growth and high biomass yield, makes a great raw material for biofuel production. The conversion of Napier Grass into a viable energy source is based on anaerobic digestion principles, which are helped by microorganisms that thrive in oxygen-free settings. These microbes meticulously degrade the cellulose and other organic molecules found in Napier Grass, resulting in a combination of methane, CO2, and trace gasses. Napier Grass' resilience to diverse soil types and climates, together with its rapid development, highlight its potential as a sustainable source of biofuel generation. This plant's intrinsic energy can be used to make a clean, efficient kind of compressed bio gas. This gas is compressed to increase its usefulness and storage capacities, making it a versatile energy carrier for a wide range of applications, including household cooking and heating as well as vehicle power.
The conversion of Napier Grass into Compressed Bio Gas demonstrates not only the unique use of biomass, but also coincides with worldwide energy sustainability objectives. It offers the opportunity to diversify energy portfolios, reduce reliance on fossil fuels, and limit environmental concerns. As we go more into the mechanics of this process, the importance of using Napier Grass as a substrate for bioenergy production becomes clearer, demonstrating its part in the larger story of renewable energy development.
Applications
-
- Transportation Fuel: As a cleaner-burning alternative to fossil fuels, CBG exhibits significant potential to power vehicles. It could provide a similar experience for drivers while reducing greenhouse gas emissions.
-
- Industrial Use: CBG's applications in industry include power generation, use in heating systems, and as a general energy source throughout manufacturing.
-
- Cooking Fuel: In places with limited infrastructure, particularly rural or remote areas, CBG could be a safer and more sustainable alternative to traditional cooking fuels like LPG (liquified petroleum gas) or kerosene.
-
- Electricity Generation: CBG can be a renewable source of energy to power gas engines or turbines. This makes it versatile for both large-scale electrical grids and independent power systems.
Method of Production
There are various processes involved in turning Napier Grass into compressed bio gas (CBG), and each one is essential to guaranteeing that biomass is efficiently converted into a clean, renewable energy source. This is a thorough breakdown of the production procedure:
1. Feed Receipt: After being collected, Napier Grass is delivered to the manufacturing plant. The grass is checked for quality and quantity upon arrival to make sure it satisfies the requirements for the production of biogas.
2. Handling and Storage Section: To preserve its quality and shield it from the weather, the received Napier Grass is kept in a special location. To stop spoiling and provide a consistent supply to the feed preparation area, proper handling is essential.
3. Feeding System and Feed Preparation: To make digestion easier, the stored Napier Grass is broken into smaller pieces. The prepared feed is then continually delivered into the anaerobic digester via a conveyance system, which is commonly automated to maintain a steady feed rate and optimum gas production.
4. Anaerobic Digester for Storing Raw Biogas: Without oxygen, bacteria in the anaerobic digester break down the biomass to produce biogas. The main ingredients of this biogas are carbon dioxide and methane. To maximize biogas generation, the digester is kept at particular parameters (temperature, pH, and retention period). After that, the digester's associated tanks are used to temporarily store the raw biogas.
5. Biogas Upgrading: Storage and Purification: A purification procedure is used to the raw biogas in order to eliminate contaminants including moisture, carbon dioxide, and hydrogen sulphide. Methane is more concentrated after this upgrading procedure, which qualifies it for usage as CBG. Next, the cleaned biogas is compressed and kept in high-pressure storage containers.
6. Bottled CBG: Following compression, the biogas is sent to bottling facilities where it is bottled under intense pressure into cylinders for sale and distribution. To guarantee quality and safety, leaks and integrity are examined in the bottles.
7. Cascade Dispatch and Storage: CBG in bottles is kept in cascade storage systems, which enable compressed gas to be stored in large volumes. After this, depending on demand, the bottles are shipped directly to consumers or to the market.
8. Organic Fertiliser Unit: A nutrient-rich sludge that is produced as a byproduct of anaerobic digestion can be converted into organic fertiliser through additional processing. This fertiliser is useful for agricultural purposes since it completes the cycle of biomass use and adds another source of income.
9. Energy Production from the Installation of Solar Plants: The facility can set up a solar plant to increase sustainability and save operating expenses. The facility's feed preparation and biogas upgrading systems, among other functions, can be powered by the electricity produced by the solar plant.
Global Market Outlook
The global Biogas Compression Market was valued at USD 24.63 billion in 2022 and is projected to reach USD 76.24 billion by 2030, growing at a CAGR of 15.41% from 2023 to 2030. The global biogas compression market is expected to grow significantly in the next years, driven by a number of factors that are increasing demand for sustainable energy solutions. Biogas, created from biological waste materials, is a greener alternative to traditional fossil fuels that adheres to severe environmental standards and sustainability goals. As countries throughout the world accelerate their efforts to reduce carbon emissions and migrate to renewable energy sources, biogas has emerged as a key actor in the global energy scene.
The market's growing trend is aided by technological developments in biogas compression systems. Compression technology innovations improve efficiency, dependability, and cost-effectiveness, addressing long-standing difficulties with biogas consumption. Governments and commercial groups are making significant investments in infrastructure development, pushing biogas incorporation into mainstream electricity networks.
Asia-Pacific is expected to be the fastest-growing area from 2023 to 2030, driven by rising energy demand and a growing emphasis on sustainable practices. Rapid industrialization, combined with increased environmental awareness, is driving the deployment of biogas compression systems. Government measures and incentives in nations such as China and India encourage investments in renewable energy, fostering industry growth. Furthermore, the region's extensive agricultural industry provides plenty of feedstock for biogas generation. With an increasing emphasis on lowering carbon footprints, the Asia-Pacific biogas compression market offers unrivaled growth potential, drawing investment and driving innovation.
Conclusion
The creation of green jobs in farming, maintenance, and operations can boost local economies when a CBG unit using Napier Grass is established. By decreasing reliance on fossil fuels, it provides a sustainable renewable energy source that also promotes energy independence. It is possible to move closer to a more economically and environmentally friendly energy landscape by using Napier Grass for CBG production.
Key Players
- Aerzen
- Air Liquide Energies
- Atlas Copco AB
- EnviTec Biogas AG
- Gazpack
- Mehrer Compression GmbH
- Reliance Industries Limited
- Wartsila
- NEUMAN & ESSER GROUP
- HAUG Sauer Kompressoren AG
Plant capacity | Plant & machinery | Working capital | Cost of Project | T.C.I | Return | Break even |
---|---|---|---|---|---|---|
Compressed Bio Gas 5 MT Per Day, By Product Liquid Fertilizer 53 MT Per Day, By Product Dry Solid Fertilizer 21 MT Per Day | 11 Cr | 0 | 28 Cr | 0 | 28.00% | 45.00% |
Introduction
We can provide you detailed project reports on the following topics. Please select the projects of your interests.
Each detailed project reports cover all the aspects of business, from analysing the market, confirming availability of various necessities such as plant & machinery, raw materials to forecasting the financial requirements. The scope of the report includes assessing market potential, negotiating with collaborators, investment decision making, corporate diversification planning etc. in a very planned manner by formulating detailed manufacturing techniques and forecasting financial aspects by estimating the cost of raw material, formulating the cash flow statement, projecting the balance sheet etc.
We also offer self-contained Pre-Investment and Pre-Feasibility Studies, Market Surveys and Studies, Preparation of Techno-Economic Feasibility Reports, Identification and Selection of Plant and Machinery, Manufacturing Process and or Equipment required, General Guidance, Technical and Commercial Counseling for setting up new industrial projects on the following topics.
Many of the engineers, project consultant & industrial consultancy firms in India and worldwide use our project reports as one of the input in doing their analysis.
- One Lac / Lakh / Lakhs is equivalent to one hundred thousand (100,000)
- One Crore is equivalent to ten million (10,000,000)
- T.C.I is Total Capital Investment
- We can modify the project capacity and project cost as per your requirement.
- We can also prepare project report on any subject as per your requirement.
- Caution: The project's cost, capacity and return are subject to change without any notice. Future projects may have different values of project cost, capacity or return.
COST OF PROJECT | MEANS OF FINANCE | ||||||
---|---|---|---|---|---|---|---|
Particulars | Existing | Proposed | Total | Particulars | Existing | Proposed | Total |
Land & Site Development Exp. | ********** | ********** | ********** | Capital | ********** | ********** | ********** |
Buildings | ********** | ********** | ********** | Share Premium | ********** | ********** | ********** |
Plant & Machineries | ********** | ********** | ********** | Other Type Share Capital | ********** | ********** | ********** |
Motor Vehicles | ********** | ********** | ********** | Reserves & Surplus | ********** | ********** | ********** |
Office Automation Equipments | ********** | ********** | ********** | Cash Subsidy | ********** | ********** | ********** |
Technical Knowhow Fees & Exp. | ********** | ********** | ********** | Internal Cash Accruals | ********** | ********** | ********** |
Franchise & Other Deposits | ********** | ********** | ********** | Long/Medium Term Borrowings | ********** | ********** | ********** |
Preliminary & Pre-operative Exp | ********** | ********** | ********** | Debentures / Bonds | ********** | ********** | ********** |
Provision for Contingencies | ********** | ********** | ********** | Unsecured Loans/Deposits | ********** | ********** | ********** |
Margin Money - Working Capital | ********** | ********** | ********** | ********** | ********** | ********** | ********** |
Total | ********** | ********** | ********** | Total | ********** | ********** | ********** |
PARTICULARS | OPERATING YEARS | ||||
---|---|---|---|---|---|
1-2 | 2-3 | 3-4 | 4-5 | 5-6 | |
********** | ********** | ********** | ********** | ********** | |
Revenue/Income/Realisation | ********** | ********** | ********** | ********** | ********** |
Gross Sales Realisation | ********** | ********** | ********** | ********** | ********** |
Less : Excise Duties/Levies | ********** | ********** | ********** | ********** | ********** |
Net Sales Realisation | ********** | ********** | ********** | ********** | ********** |
Total Revenue/Income/Realisation | ********** | ********** | ********** | ********** | ********** |
********** | ********** | ********** | ********** | ********** | |
Expenses/Cost of Products/Services/Items | ********** | ********** | ********** | ********** | ********** |
Raw Material Cost | ********** | ********** | ********** | ********** | ********** |
Indigenous | ********** | ********** | ********** | ********** | ********** |
Total Nett Consumption | ********** | ********** | ********** | ********** | ********** |
Lab & ETP Chemical Cost | ********** | ********** | ********** | ********** | ********** |
Packing Material Cost | ********** | ********** | ********** | ********** | ********** |
Sub Total of Net Consumption | ********** | ********** | ********** | ********** | ********** |
Miscellaneous Cost | ********** | ********** | ********** | ********** | ********** |
Employees Expenses | ********** | ********** | ********** | ********** | ********** |
Fuel Expenses | ********** | ********** | ********** | ********** | ********** |
Power/Electricity Expenses | ********** | ********** | ********** | ********** | ********** |
Depreciation | ********** | ********** | ********** | ********** | ********** |
Royalty & Other Charges | ********** | ********** | ********** | ********** | ********** |
Repairs & Maintenance Exp. | ********** | ********** | ********** | ********** | ********** |
Other Mfg. Expenses | ********** | ********** | ********** | ********** | ********** |
Cost of Output of Goods Sold | ********** | ********** | ********** | ********** | ********** |
********** | ********** | ********** | ********** | ********** | |
Gross Profit | ********** | ********** | ********** | ********** | ********** |
Administration Expenses | ********** | ********** | ********** | ********** | ********** |
Technical Knowhow Fees & Exp. | ********** | ********** | ********** | ********** | ********** |
Financial Charges | ********** | ********** | ********** | ********** | ********** |
Long/Medium Term Borrowing | ********** | ********** | ********** | ********** | ********** |
On Wkg. Capital Borrowings | ********** | ********** | ********** | ********** | ********** |
Total Financial Charges | ********** | ********** | ********** | ********** | ********** |
Selling Expenses | ********** | ********** | ********** | ********** | ********** |
Total Cost of Sales | ********** | ********** | ********** | ********** | ********** |
********** | ********** | ********** | ********** | ********** | |
Net Profit Before Taxes | ********** | ********** | ********** | ********** | ********** |
Tax on Profit | ********** | ********** | ********** | ********** | ********** |
Net Profit After Taxes | ********** | ********** | ********** | ********** | ********** |
Depreciation Added Back | ********** | ********** | ********** | ********** | ********** |
Technical Knowhow Fees & Exp. | ********** | ********** | ********** | ********** | ********** |
Net Cash Accruals | ********** | ********** | ********** | ********** | ********** |
PARTICULARS | EXISTING | PROPOSED | TOTAL |
---|---|---|---|
COST OF PROJECT | |||
Land & Site Development Exp. | |||
Land Area Required | ********** | ********** | ********** |
Land Development Cost, Boundary Wall, Gate & Road etc. | ********** | ********** | ********** |
********** | ********** | ********** | |
Buildings | ********** | ********** | ********** |
Factory Building - | ********** | ********** | ********** |
Office Buildings | ********** | ********** | ********** |
********** | ********** | ********** | |
Plant & Machineries | ********** | ********** | ********** |
Indigenous Machineries | ********** | ********** | ********** |
Erection & Installation | ********** | ********** | ********** |
Laboratory Equipments | ********** | ********** | ********** |
Miscellaneous Equipments like pumps, valves, pipeline & fittings | ********** | ********** | ********** |
Imported Machineries | ********** | ********** | ********** |
Technical know how | ********** | ********** | ********** |
********** | ********** | ********** | |
Office Vehicles | ********** | ********** | ********** |
Office Automation Equipments (Telephone/ Fax/ Computer) | ********** | ********** | ********** |
Office Equipment, Furniture plus Other Equipment & Accessories | ********** | ********** | ********** |
Other Misc. Assets | ********** | ********** | ********** |
********** | ********** | ********** | |
Pre-operative & Preliminary Expenses | ********** | ********** | ********** |
Provision for Contingencies | ********** | ********** | ********** |
********** | ********** | ********** | |
Total Capital Cost of Project | ********** | ********** | ********** |
Margin Money for Working Capital | ********** | ********** | ********** |
Total Cost of Project | ********** | ********** | ********** |
PARTICULARS | STK.PRD. | STK.PRD. | OPERATING YEARS | |||||
---|---|---|---|---|---|---|---|---|
1st Year | 2nd Yr &+ | 1-2 | 2-3 | 3-4 | 4-5 | 5-6 | ||
Capacity | Months | Months | % | ********** | ********** | ********** | ********** | ********** |
CURRENT ASSETS | ********** | ********** | ********** | ********** | ********** | |||
Stocks on Hand | ********** | ********** | ********** | ********** | ********** | |||
Raw Material Cost | ********** | ********** | ********** | ********** | ********** | |||
Indigenous | ********** | ********** | M | ********** | ********** | ********** | ********** | ********** |
Lab & ETP Chemical | ********** | ********** | M | ********** | ********** | ********** | ********** | ********** |
Packing Material | ********** | ********** | M | ********** | ********** | ********** | ********** | ********** |
Consumable Store | ********** | ********** | M | ********** | ********** | ********** | ********** | ********** |
Work-in-Process | ********** | ********** | D | ********** | ********** | ********** | ********** | ********** |
Finished Goods | ********** | ********** | M | ********** | ********** | ********** | ********** | ********** |
Current Expenses | ********** | ********** | M | ********** | ********** | ********** | ********** | ********** |
Receivables | ********** | ********** | M | ********** | ********** | ********** | ********** | ********** |
********** | ********** | ********** | ********** | ********** | ********** | ********** | ||
Total | ********** | ********** | ********** | ********** | ********** | |||
Cash/Bank Balances | ********** | ********** | ********** | ********** | ********** | |||
Gross Wkg. Capital | ********** | ********** | ********** | ********** | ********** |
PARTICULARS | OPERATING YEARS | |||||
---|---|---|---|---|---|---|
1-2 | 2-3 | 3-4 | 4-5 | 5-6 | ||
Profit Percentages to Net Sales | ||||||
Gross Profit | ********** | ********** | ********** | ********** | ********** | |
% Of G.P. to Net Sales | ********** | ********** | ********** | ********** | ********** | |
Net Profit Before Taxes | ********** | ********** | ********** | ********** | ********** | |
% of N.P.B.T. To Net Sales | ********** | ********** | ********** | ********** | ********** | |
Net Profit After Taxes | ********** | ********** | ********** | ********** | ********** | |
% of N.P.A.T. To Net Sales | ********** | ********** | ********** | ********** | ********** | |
Debt Service Coverage Ratio | ********** | ********** | ********** | ********** | ********** | |
Debt Service Coverage Ratio | ||||||
Funds Available to Service Debts | ||||||
Net Profit After Taxes | ********** | ********** | ********** | ********** | ********** | |
Depreciation Charges | ********** | ********** | ********** | ********** | ********** | |
Technical Knowhow Fees & Exp | ********** | ********** | ********** | ********** | ********** | |
Interest on Long/Medium Term | ********** | ********** | ********** | ********** | ********** | |
Total | ********** | ********** | ********** | ********** | ********** | |
Debt Service Obligations | ||||||
Repayment of Long/Medium Term | ********** | ********** | ********** | ********** | ********** | |
Interest on Long/Medium Term | ********** | ********** | ********** | ********** | ********** | |
Total | ********** | ********** | ********** | ********** | ********** | |
********** | ********** | ********** | ********** | ********** | ||
D. S. C. R. (Individual) | ********** | ********** | ********** | ********** | ********** | |
D. S. C. R. (Cumulative) | ********** | ********** | ********** | ********** | ********** | |
D. S. C. R. (Overall) | ********** | ********** | ********** | ********** | ********** | |
Parameters | ||||||
Initial Equity Capital | ********** | ********** | ********** | ********** | ********** | ********** |
Credit Balance in P & L | ********** | ********** | ********** | ********** | ********** | ********** |
Total Capital exclUnsec Deposits | ********** | ********** | ********** | ********** | ********** | ********** |
Unsecured Dep. | ********** | ********** | ********** | ********** | ********** | ********** |
Total Equity incl Unsecured Deposits | ********** | ********** | ********** | ********** | ********** | ********** |
Long/Medium Term Borrowings from Bank | ********** | ********** | ********** | ********** | ********** | ********** |
Term lia. Incl Unsecured Deposit | ********** | ********** | ********** | ********** | ********** | ********** |
Total Liabilities | ********** | ********** | ********** | ********** | ********** | ********** |
Total Liabilities incl Unsecured Deposits | ********** | ********** | ********** | ********** | ********** | ********** |
DEBT EQUITY RATIO considering | ********** | ********** | ********** | ********** | ********** | ********** |
DEBT EQUITY RATIO considering | ||||||
I.E.Total Term Lia./NW | ||||||
Unsecured Dep. as Equity | ********** | ********** | ********** | ********** | ********** | ********** |
Unsecured Dep. as Debt | ********** | ********** | ********** | ********** | ********** | ********** |
Total Outside Lia./NW | ********** | ********** | ********** | ********** | ********** | ********** |
Total Outside Lia./NW | ********** | ********** | ********** | ********** | ********** | |
Assets Turnover Ratio (x) | ********** | ********** | ********** | ********** | ********** | |
No. of Shares of 10.00 each | ********** | ********** | ********** | ********** | ********** | |
Earnings Per Share (EPS) (in) | ********** | ********** | ********** | ********** | ********** | |
Proposed divident | ********** | ********** | ********** | ********** | ********** | |
Cash EPS (in) | ********** | ********** | ********** | ********** | ********** | |
Dividend Per Share(DPS) (in) | ********** | ********** | ********** | ********** | ********** | |
Payout Ratio (%Age) | ********** | ********** | ********** | ********** | ********** | |
Retained Earnings/Share (in) | ********** | ********** | ********** | ********** | ********** | |
Retained Earnings (%Age) | ********** | ********** | ********** | ********** | ********** | |
Book Value Per Share (in) | ********** | ********** | ********** | ********** | ********** | |
Debt Per Share (in) | ********** | ********** | ********** | ********** | ********** | |
Probable Mkt. Price/Share(in) | ********** | ********** | ********** | ********** | ********** | |
Price / Book Value (x) | ********** | ********** | ********** | ********** | ********** | |
Price Earnings Ratio (x) | ********** | ********** | ********** | ********** | ********** | |
Yield (%Age) | ********** | ********** | ********** | ********** | ********** |
PARTICULARS | OPERATING YEARS | |||||
---|---|---|---|---|---|---|
Ratio | 1-2 | 2-3 | 3-4 | 4-5 | 5-6 | |
BREAK EVEN ANALYSIS | ||||||
Total Value of Output | ********** | ********** | ********** | ********** | ********** | |
Variable Cost & Expenses | ||||||
Raw Material Cost | ********** | ********** | ********** | ********** | ********** | ********** |
Lab & ETP Chemical Cost | ********** | ********** | ********** | ********** | ********** | ********** |
Packing Material Cost | ********** | ********** | ********** | ********** | ********** | ********** |
Sales Commission/Exp. | ********** | ********** | ********** | ********** | ********** | ********** |
Sub-total | ********** | ********** | ********** | ********** | ********** | |
Less: W.I.P. Adjustments | ********** | ********** | ********** | ********** | ********** | |
Total Variable Cost | ********** | ********** | ********** | ********** | ********** | |
Net Contribution | ********** | ********** | ********** | ********** | ********** | |
Profit Volume Ratio (%) | ********** | ********** | ********** | ********** | ********** | |
Semi-Var./Semi-Fixed Exp. | ********** | ********** | ********** | ********** | ********** | ********** |
Miscellaneous Cost | ********** | ********** | ********** | ********** | ********** | ********** |
Employees Expenses | ********** | ********** | ********** | ********** | ********** | ********** |
Power/Electricity Expen | ********** | ********** | ********** | ********** | ********** | ********** |
Fuel Expenses | ********** | ********** | ********** | ********** | ********** | ********** |
Royalty & Other Charges | ********** | ********** | ********** | ********** | ********** | ********** |
Repairs & Maintenance E | ********** | ********** | ********** | ********** | ********** | ********** |
Other Mfg. Expenses | ********** | ********** | ********** | ********** | ********** | ********** |
Administration Expenses | ********** | ********** | ********** | ********** | ********** | ********** |
Selling Expenses | ********** | ********** | ********** | ********** | ********** | ********** |
Interest on Wkg.Capital | ********** | ********** | ********** | ********** | ********** | ********** |
Tot.Semi-Var./Fixed Exp. | ********** | ********** | ********** | ********** | ********** | ********** |
Fixed Expenses / Cost | ********** | ********** | ********** | ********** | ********** | ********** |
Miscellaneous Cost | ********** | ********** | ********** | ********** | ********** | ********** |
Employees Expenses | ********** | ********** | ********** | ********** | ********** | ********** |
Power/Electricity Expen | ********** | ********** | ********** | ********** | ********** | ********** |
Fuel Expenses | ********** | ********** | ********** | ********** | ********** | ********** |
Royalty & Other Charges | ********** | ********** | ********** | ********** | ********** | ********** |
Repairs & Maintenance E | ********** | ********** | ********** | ********** | ********** | ********** |
Other Mfg. Expenses | ********** | ********** | ********** | ********** | ********** | ********** |
Administration Expenses | ********** | ********** | ********** | ********** | ********** | ********** |
Selling Expenses | ********** | ********** | ********** | ********** | ********** | ********** |
Intrest-Fixed Borrowing | ********** | ********** | ********** | ********** | ********** | ********** |
Intrest-Working Capital | ********** | ********** | ********** | ********** | ********** | ********** |
Depreciation Charges | ********** | ********** | ********** | ********** | ********** | ********** |
Deferred Expenses W/Off | ********** | ********** | ********** | ********** | ********** | ********** |
Total Fixed Expenses | ********** | ********** | ********** | ********** | ********** | ********** |
Tot.Fixed/Semi-Fixed Exp | ********** | ********** | ********** | ********** | ********** | ********** |
Tot.Cash Fixed/SemiFixed | ********** | ********** | ********** | ********** | ********** | ********** |
Cash Break Even Sales | ********** | ********** | ********** | ********** | ********** | ********** |
Cash Margin of Safety | ********** | ********** | ********** | ********** | ********** | ********** |
Break Even Sales | ********** | ********** | ********** | ********** | ********** | ********** |
Margin of safety | ********** | ********** | ********** | ********** | ********** | ********** |
At Maximum Utilisation : | Year | ********** | ********** | ********** | ********** | ********** |
(as % of Installed Capacity) | ||||||
Cash B.E.P. : | % | xx% | xx% | xx% | xx% | xx% |
B.E.P. : | % | xx% | xx% | xx% | xx% | xx% |
MEANS OF FINANCE | |||
---|---|---|---|
Equity Share Capital | ********** | ********** | ********** |
Others - Preference Share Capital | ********** | ********** | ********** |
Total Equity Share Capital | ********** | ********** | ********** |
********** | ********** | ********** | |
Long/Medium Term Borrowings | ********** | ********** | ********** |
FROM BANK | ********** | ********** | ********** |
From Other Financial Institutions | ********** | ********** | ********** |
Total Long/Medium Term Borrowings | ********** | ********** | ********** |
********** | ********** | ********** | |
Total Means of Finance | ********** | ********** | ********** |
PARTICULARS | OPERATING YEARS | ||||
---|---|---|---|---|---|
1-2 | 2-3 | 3-4 | 4-5 | 5-6 | |
Equity Share Capital | ********** | ********** | ********** | ********** | ********** |
Surplus of Previous Year | ********** | ********** | ********** | ********** | ********** |
Add : Net Profit After Taxes | ********** | ********** | ********** | ********** | ********** |
Surplus at the End of Year | ********** | ********** | ********** | ********** | ********** |
Unsecured Deposits | ********** | ********** | ********** | ********** | ********** |
Long/Medium Term Borrowings Proposed-FROM BANK | ********** | ********** | ********** | ********** | ********** |
Bank Borrowing for Wkg. Capital | ********** | ********** | ********** | ********** | ********** |
Current Liabilities | ********** | ********** | ********** | ********** | ********** |
Sundry Creditors | ********** | ********** | ********** | ********** | ********** |
Other Current Liabilities | ********** | ********** | ********** | ********** | ********** |
Total Current Liabilities | ********** | ********** | ********** | ********** | ********** |
********** | ********** | ********** | ********** | ********** | |
Total of Liabilities | ********** | ********** | ********** | ********** | ********** |
********** | ********** | ********** | ********** | ********** | |
ASSETS | ********** | ********** | ********** | ********** | ********** |
Fixed Assets | ********** | ********** | ********** | ********** | ********** |
Gross Block | ********** | ********** | ********** | ********** | ********** |
Less : Depreciation to Date | ********** | ********** | ********** | ********** | ********** |
Net Block | ********** | ********** | ********** | ********** | ********** |
Current Assets | ********** | ********** | ********** | ********** | ********** |
Stocks on Hand | ********** | ********** | ********** | ********** | ********** |
Receivables | ********** | ********** | ********** | ********** | ********** |
Other Current Assets | ********** | ********** | ********** | ********** | ********** |
Cash and Bank Balances | ********** | ********** | ********** | ********** | ********** |
Total Current Assets | ********** | ********** | ********** | ********** | ********** |
P & P Exp. and/or Other Dvp.Exp. | ********** | ********** | ********** | ********** | ********** |
(To The Extent Not W/Off) | ********** | ********** | ********** | ********** | ********** |
Other Non Current Assets | ********** | ********** | ********** | ********** | ********** |
********** | ********** | ********** | ********** | ********** | |
Total of Assets | ********** | ********** | ********** | ********** | ********** |
ROI (Average of Fixed Assets) | ********** | ********** | ********** | ********** | ********** |
RONW (Average of Share Capital) | ********** | ********** | ********** | ********** | ********** |
ROI (Average of Total Assets) | ********** | ********** | ********** | ********** | ********** |
INTEREST AND REPAYMENT ON TERM LOANS
A | Name of Institution-Bank | ABC BANK | |
---|---|---|---|
B | Term Borrowing Amount | ********** | xx |
C | Repayment Term (Years) | ********** | Years |
D | Repayment Instalments | ********** | Instalments |
E | Repayment Commencement | Year - 0; 3rd Qtr. | |
F | Rate of Interest(General) | xxxx% | p.a. |
G | Rate of Interest(Initial) | 0.00% | p.a. |
H | Apply Gen. Int. Rate from Year | x Quarter :: x | |
I | Interest Calculation | Quarterly |
Debt Service Coverage Ratio | ||||||
---|---|---|---|---|---|---|
Funds Available to Service Debts | ||||||
Net Profit After Taxes | ********** | ********** | ********** | ********** | ********** | |
Depreciation Charges | ********** | ********** | ********** | ********** | ********** | |
Technical Knowhow Fees & Expenses | ********** | ********** | ********** | ********** | ********** | |
Interest on Long/Medium Term | ********** | ********** | ********** | ********** | ********** | |
Total | ********** | ********** | ********** | ********** | ********** | |
Debt Service Obligations | ********** | ********** | ********** | ********** | ********** | |
Repayment of Long/Medium Term | ********** | ********** | ********** | ********** | ********** | |
Interest on Long/Medium Term | ********** | ********** | ********** | ********** | ********** | |
Total | ********** | ********** | ********** | ********** | ********** | |
********** | ********** | ********** | ********** | ********** | ||
D. S. C. R. (Individual) | ********** | ********** | ********** | ********** | ********** | |
D. S. C. R. (Cumulative) ..... | ********** | ********** | ********** | ********** | ********** | |
D. S. C. R. (Overall) ........ | ********** | ********** | ********** | ********** | ********** |
DEPRECIATION CHARGES AS PER BOOKS (TOTAL)
Operating Year | F.Assets Type A-1 | F.Assets Type A-2 | F.Assets Type B | F.Assets Type C | F.Assets Type D-1 | F.Assets Type D-2 | Total |
---|---|---|---|---|---|---|---|
Particulars | Factory Building | Office Buildings | Plant & Machinery | Office Vehicles | Office Automation Equipments (Telephone/ Fax/ Computer) | Furniture & Fixtures | |
1-2 | ********** | ********** | ********** | ********** | ********** | ********** | ********** |
********** | ********** | ********** | ********** | ********** | ********** | ********** | |
********** | ********** | ********** | ********** | ********** | ********** | ********** | |
2-3 | ********** | ********** | ********** | ********** | ********** | ********** | ********** |
********** | ********** | ********** | ********** | ********** | ********** | ********** | |
********** | ********** | ********** | ********** | ********** | ********** | ********** | |
3-4 | ********** | ********** | ********** | ********** | ********** | ********** | ********** |
********** | ********** | ********** | ********** | ********** | ********** | ********** | |
********** | ********** | ********** | ********** | ********** | ********** | ********** | |
4-5 | ********** | ********** | ********** | ********** | ********** | ********** | ********** |
********** | ********** | ********** | ********** | ********** | ********** | ********** | |
********** | ********** | ********** | ********** | ********** | ********** | ********** | |
5-6 | ********** | ********** | ********** | ********** | ********** | ********** | ********** |
********** | ********** | ********** | ********** | ********** | ********** | ********** | |
********** | ********** | ********** | ********** | ********** | ********** | ********** |
Particulars | Method | Deprn.Rate | Part Consideration (for Asset put to use less than xx months) |
---|---|---|---|
Type A :: Buildings | |||
Factory Building - | WDV | ********** | ********** |
Office Buildings | WDV | ********** | ********** |
Type C | |||
Office Vehicles | WDV | ********** | ********** |
Type D :: Misc. Fixed Assets | |||
Office Automation Equipments (Telephone/ Fax/ Computer) | WDV | ********** | ********** |
Furniture & Fixtures | WDV | ********** | ********** |
Type B :: Plant & Machineries |
Projected Pay Back Period | |||||
---|---|---|---|---|---|
Particulars | Operating Years | ||||
1-2 | 2-3 | 3-4 | 4-5 | 5-6 | |
Year | 1 | 2 | 3 | 4 | 5 |
Initial Investment | ********* | ||||
Total Initial Investment | ********* | ||||
Yearly Cash Flow | ********* | ********* | ********* | ********* | ********* |
Accumulated Cash Flow | ********* | ********* | ********* | ********* | ********* |
Accumulated Cash Flow | ********* | ********* | ********* | ********* | ********* |
Pay Back Period | xx Years xx Months | xx Years xx months |
Projected IRR | |||||
---|---|---|---|---|---|
Year | CFAT | PV factor @**% | ********* | ||
Initial Investment | ********* | ********* | ********* | ||
1-2 | ********* | ********* | ********* | ||
2-3 | ********* | ********* | ********* | ||
3-4 | ********* | ********* | ********* | ||
4-5 | ********* | ********* | ********* | ||
5-6 | ********* | ********* | ********* | ||
Total PV | ********* | ********* | |||
IRR | ********* | ********* | |||
NIIR PROJECT CONSULTANCY SERVICES (NPCS) is a reliable name in the industrial world for offering integrated technical consultancy services. NPCS is manned by engineers, planners, specialists, financial experts, economic analysts and design specialists with extensive experience in the related industries.
Our various services are: Detailed Project Report, Business Plan for Manufacturing Plant, Start-up Ideas, Business Ideas for Entrepreneurs, Start up Business Opportunities, entrepreneurship projects, Successful Business Plan, Industry Trends, Market Research, Manufacturing Process, Machinery, Raw Materials, project report, Cost and Revenue, Pre-feasibility study for Profitable Manufacturing Business, Project Identification, Project Feasibility and Market Study, Identification of Profitable Industrial Project Opportunities, Business Opportunities, Investment Opportunities for Most Profitable Business in India, Manufacturing Business Ideas, Preparation of Project Profile, Pre-Investment and Pre-Feasibility Study, Market Research Study, Preparation of Techno-Economic Feasibility Report, Identification and Selection of Plant, Process, Equipment, General Guidance, Startup Help, Technical and Commercial Counseling for setting up new industrial project and Most Profitable Small Scale Business.
NPCS also publishes varies process technology, technical, reference, self employment and startup books, directory, business and industry database, bankable detailed project report, market research report on various industries, small scale industry and profit making business. Besides being used by manufacturers, industrialists and entrepreneurs, our publications are also used by professionals including project engineers, information services bureau, consultants and project consultancy firms as one of the input in their research.
- This report helps you to identify a profitable project for investing or diversifying into by throwing light to crucial areas like industry size, demand of the product and reasons for investing in the product.
- This report provides vital information on the product like its definition, characteristics and segmentation.
- This report helps you market and place the product correctly by identifying the target customer group of the product.
- This report helps you understand the viability of the project by disclosing details like raw materials required, manufacturing process, project costs and snapshot of other project financials.
- The report provides forecasts of key parameters which helps to anticipate the industry performance and make sound business decision.
- Our research reports broadly cover Indian markets, present analysis, outlook and forecast.
- The market forecasts are developed on the basis of secondary research and are cross-validated through interactions with the industry players.
- We use reliable sources of information and databases. And information from such sources is processed by us and included in the report.
Introduction
- Project Introduction
- Project Objective and Strategy
- Concise History of the Product
- Properties
- BIS (Bureau of Indian Standards) Provision & Specification
- Uses & Applications
Market Study and Assessment
- Current Indian Market Scenario
- Present Market Demand and Supply
- Estimated Future Market Demand and Forecast
- Statistics of Import & Export
- Names & Addresses of Existing Units (Present Players)
- Market Opportunity
Raw Material
- List of Raw Materials
- Properties of Raw Materials
- Prescribed Quality of Raw Materials
- List of Suppliers and Manufacturers
Personnel (Manpower) Requirements
- Requirement of Staff & Labor (Skilled and Unskilled) Managerial, Technical, Office Staff and Marketing Personnel
Plant and Machinery
- List of Plant & Machinery
- Miscellaneous Items
- Appliances &Equipments
- Laboratory Equipments& Accessories
- Electrification
- Electric Load & Water
- Maintenance Cost
- Sources of Plant & Machinery (Suppliers and Manufacturers)
Manufacturing Process and Formulations
- Detailed Process of Manufacture with Formulation
- Packaging Required
- Process Flow Sheet Diagram
Infrastructure and Utilities
- Project Location
- Requirement of Land Area
- Rates of the Land
- Built Up Area
- Construction Schedule
- Plant Layout and Requirement of Utilities
- Assumptions for Profitability workings
- Plant Economics
- Production Schedule
-
- Land & Building
- Factory Land & Building
- Site Development Expenses
-
- Plant & Machinery
- Indigenous Machineries
- Other Machineries (Miscellaneous, Laboratory etc.)
-
- Other Fixed Assets
- Furniture & Fixtures
- Pre-operative and Preliminary Expenses
- Technical Knowhow
- Provision of Contingencies
-
- Working Capital Requirement Per Month
- Raw Material
- Packing Material
- Lab & ETP Chemical Cost
- Consumable Store
-
- Overheads Required Per Month And Per Annum
- Utilities & Overheads (Power, Water and Fuel Expenses etc.)
- Royalty and Other Charges
- Selling and Distribution Expenses
- Salary and Wages
- Turnover Per Annum
-
- Share Capital
- Equity Capital
- Preference Share Capital
- Annexure 1:: Cost of Project and Means of Finance
-
- Annexure 2:: Profitability and Net Cash Accruals
- Revenue/Income/Realisation
- Expenses/Cost of Products/Services/Items
- Gross Profit
- Financial Charges
- Total Cost of Sales
- Net Profit After Taxes
- Net Cash Accruals
-
- Annexure 3 :: Assessment of Working Capital requirements
- Current Assets
- Gross Working. Capital
- Current Liabilities
- Net Working Capital
- Working Note for Calculation of Work-in-process
- Annexure 4 :: Sources and Disposition of Funds
-
- Annexure 5 :: Projected Balance Sheets
- ROI (Average of Fixed Assets)
- RONW (Average of Share Capital)
- ROI (Average of Total Assets)
-
- Annexure 6 :: Profitability ratios
- D.S.C.R
- Earnings Per Share (EPS)
- Debt Equity Ratio
-
- Annexure 7 :: Break-Even Analysis
- Variable Cost & Expenses
- Semi-Var./Semi-Fixed Exp.
- Profit Volume Ratio (PVR)
- Fixed Expenses / Cost
- B.E.P
-
- Annexure 8 to 11:: Sensitivity Analysis-Price/Volume
- Resultant N.P.B.T
- Resultant D.S.C.R
- Resultant PV Ratio
- Resultant DER
- Resultant ROI
- Resultant BEP
-
- Annexure 12 :: Shareholding Pattern and Stake Status
- Equity Capital
- Preference Share Capital
-
- Annexure 13 :: Quantitative Details-Output/Sales/Stocks
- Determined Capacity P.A of Products/Services
- Achievable Efficiency/Yield % of Products/Services/Items
- Net Usable Load/Capacity of Products/Services/Items
- Expected Sales/ Revenue/ Income of Products/ Services/ Items
- Annexure 14 :: Product wise domestic Sales Realisation
- Annexure 15 :: Total Raw Material Cost
- Annexure 16 :: Raw Material Cost per unit
- Annexure 17 :: Total Lab & ETP Chemical Cost
- Annexure 18 :: Consumables, Store etc.,
- Annexure 19 :: Packing Material Cost
- Annexure 20 :: Packing Material Cost Per Unit
- Annexure 21 :: Employees Expenses
- Annexure 22 :: Fuel Expenses
- Annexure 23 :: Power/Electricity Expenses
- Annexure 24 :: Royalty & Other Charges
- Annexure 25 :: Repairs & Maintenance Exp.
- Annexure 26 :: Other Mfg. Expenses
- Annexure 27 :: Administration Expenses
- Annexure 28 :: Selling Expenses
- Annexure 29 :: Depreciation Charges – as per Books (Total)
- Annexure 30 :: Depreciation Charges – as per Books (P & M)
- Annexure 31 :: Depreciation Charges - As per IT Act WDV (Total)
- Annexure 32 :: Depreciation Charges - As per IT Act WDV (P & M)
- Annexure 33 :: Interest and Repayment - Term Loans
- Annexure 34 :: Tax on Profits
- Annexure 35 ::Projected Pay-Back Period And IRR
- One Lac / Lakh / Lakhs is equivalent to one hundred thousand (100,000)
- One Crore is equivalent to ten million (10,000,000)
- T.C.I is Total Capital Investment
- We can modify the project capacity and project cost as per your requirement.
- We can also prepare project report on any subject as per your requirement.
- Caution: The project's cost, capacity and return are subject to change without any notice. Future projects may have different values of project cost, capacity or return.
Need assistance?
Share your details, we will call you
NIIR PROJECT CONSULTANCY SERVICES (NPCS) is a reliable name in the industrial world for offering integrated technical consultancy services.
Read more →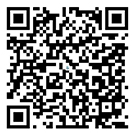
Quick Links
Products & Services
Contact Info
106-E, Kamla Nagar,
New Delhi-110007, India. |
|
+91 9097-075-054, +91-11-23843955 Any quries? Call us. |
|
[email protected]
Any quries? Mail Now. |
- Copyright © 2000-2025 NPCS, All Right Reserved.
X
Have a business idea? Let’s make it
happen together-contact us now!