
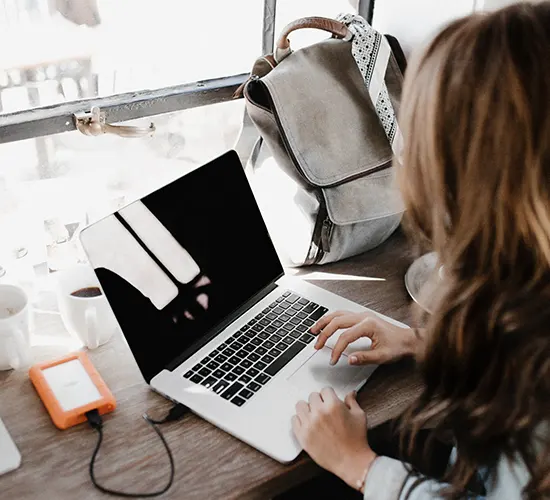
Google Search

A well-documented Business Plan aids in business funding and it is proven to help businesses grow by 30% faster.

Test Your Business ideas- We clear your doubts on Business concept and validate it properly. Often Businesses fail when the Business Plan is weak.

Market Research & High Industry Demand- We will analyse the Market Potential for optimal Industry Growth.
- Overview
- Stats
- Introduction
- Information
- Contact Us
- Project At A Glance
- Profitability And Net Cash Accruals
- Cost Of Project
- Asssessement Of Working Capital Requirements
- Profitability Ratios, Dscr, Debt Equity
- Break Even Analysis
- Means Of Finance
- Projected Balance Sheet
- Repayment Of Term Loan
- Debt Service Coverage Ratio
- Depreciation Chart
- Projected Pay-Back Period
- Projected Irr
- Company Summary
- Reasons For Buying The Report
- Our Approach
- Table Of Content
- Financial Plan
- Information/ Disclaimer
Best Manufacturing Business To Start With 30 Million
Best Manufacturing Business To Start With 30 Million (Machinery). Profit-Making Projects for Entrepreneurs, Startups Small and Medium Enterprises sector has emerged as a highly vibrant and dynamic sector of the Indian economy and is widely acclaimed as engine of economic growth, particularly in the context of Make in India initiative of the Government of India. MSMEs play a noteworthy role in economic and social development, thereby providing flip to entrepreneurship, as they have inherent characteristics of being innovative and responsive to changing market dynamics. Being complementary to large industries this sector contributes hugely to the socioeconomic development of the country. I.V. Fluids (BFS Technology) Fluids are given when someone's body fluid volume falls. There are a number of things which can cause a drop in fluid volume. Vomiting and diarrhea are a classic example, which is why people are encouraged to drink fluids when they are sick, to keep their fluid volume stable. Another cause is blood loss, which causes problems both because people lose blood products, and because they experience a loss in fluid volume. Electrolyte levels in the blood can also become unstable as a result of rapid changes in fluid volume, in which case intravenous fluids can be used to restore the balance. Intravenous fluids are fluids which are intended to be administered to a patient intravenously, directly through the circulatory system. These fluids must be sterile to protect patients from injury, and there are a number of different types available for use. Many companies manufacture packaged intravenous fluids, as well as products which can be mixed with sterile water to prepare a solution for intravenous administration. The growth of the global intravenous solutions market is driven by several factors. The increasing incidence of gastrointestinal disorders, diabetes, and cancer is one of the major factors that are expected to increase the rate of adoption of intravenous solutions among consumers. The rising popularity of intravenous vitamin C therapy in cancer treatment is one of the major trends in the intravenous solutions market. The intravenous vitamin C solution has been observed to have an increased toxicity to cancer cells and improve the patients' quality of life. The market for Intravenous (IV) Solution is expected to reach USD 11,511.2 million by 2022 and is expected to grow at a CAGR of 7.69% during the forecast period 2016-2022. The factors which drive the growth of the market are the rising prevalence of chronic diseases, rising acceptance of vitamin C intravenous treatment therapy to treat colorectal cancer. Precipitated Silica from Rice Husk Ash Rice milling generates a byproduct known as husk. This surrounds the paddy grain. During milling of paddy about 78 % of weight is received as rice, broken rice and bran. Rest 22 % of the weight of paddy is received as husk. This husk contains about 75 % organic volatile matter and the balance 25 % of the weight of this husk is converted into ash during the firing process is known as rice husk ash (RHA). This RHA in turn contains around 85 % - 90 % amorphous silica. Precipitated silica is used as filler for paper & rubber as a carrier & diluents for agricultural chemicals, as an anti-caking agent, to control viscosity & thickness and as a cleansing agent in toothpastes & in cosmetics. Precipitated silica market, which accounts for around 70% of the global specialty silica market is expected to witness steady growth in the next three years. The rising demand for energy efficient products in the automotive industry has resulted in the rapid growth of the global precipitated silica market. As a result of these factors, the global precipitated silica market is expected to expand at a 5.5% CAGR between 2015 and 2023. The growth of silica as a market is driven by its increasing application in paints and coatings. It is mainly utilized in this industry to control rheological characteristics and to aid in the deterrence of rust and corrosion. It is also used as an anti-settling agent and thixotroping agent in the sector. A developing paints and coatings industry in the emerging markets of Asia Pacific, driven by growing construction and automotive sectors, is expected to drive product demand over the forecast period. Soft Gelatin Capsules A soft gel or soft gelatin capsule is a solid capsule (outer shell) surrounding a liquid or semi-solid center (inner fill). They are oral dosage form for medicine similar to capsules. Soft gel shells are a combination of gelatin, water, pacifier and a plasticizer such as glycerin and sorbitol(s). Soft gelatin (also called soft gel or soft elastic) capsules consist of one piece hermetically-sealed soft shells. Soft gelatin capsules are prepared by adding a plasticizer, such as glycerin or polyhydric alcohol (sorbitol) to gelatin. The plasticizer makes gelatin elastic. Soft gelatin capsules come in various shapes such as spherical, elliptical, oblong, and special tube shapes with and without twist off. They can contain non-aqueous liquids, suspensions, pasty materials, or dry powders. The term soft gelatin capsules is commonly abbreviated to soft gels. Soft gelatin capsules has an advantages over hard gelatin capsules is to make a liquid formulation containing the drug in a one-piece outer gelatin shell. The demand of the soft gel capsules is increasing due to the available customization facilities for the molds and content as per customer needs. The soft gel capsules have many application areas out of which pharmaceutical, cosmetics and health supplements contribute the major shares to the growth of the global soft gel capsules market. The Global Soft gel Capsules Market is poised to grow at a CAGR of around 5.4% over the next decade to reach approximately $316.6 billion by 2025. The Soft Gelatin Capsules industry concentration is high there are more than one hundreds manufacturers in the world and high-end products mainly from U.S. and Western European. In the world wide, giant manufactures mainly distribute in American and Europe. In order to meet the strong increasing market demand. Agricultural Warehouse with Cold Storage Storage means the phase of the post-harvest system during which the products are kept in such a way as to guarantee food security other than during periods of agricultural production. At the marketing level, to balance the supply and demand of agricultural products, thereby stabilizing market prices. Cold storage warehouse means a storage warehouse used to store fresh and frozen perishable fruits or vegetables, meat, seafood, dairy products, or fowl, or any combination thereof, at a desired temperature to maintain the quality of the product for orderly marketing. The difference between warehouse and store is that warehouse is a place for storing large amounts of products (wares) in logistics, a place where products go to from the manufacturer before going to the retailer while store is a place where items may be accumulated or routinely kept. These cold storages give perishable food items a longer shelf life by preventing them from rotting due to humidity, high temperature and micro-organisms. A cold storage facility accessible to them will go a long way in removing the risk of distress sale to ensure better returns. The market will be driven by technological advancements and rising share of organized players in the market. The growth of online grocery retail and food processing industry will further create demand for cold storage and transportation facilities as major players and chains undertake expansion across various cities in the country. The government will launch new scheme called SAMPADA for development of small and medium scale processing clusters close to the growing areas of the specific farm produce. Cold chain companies further plan to upgrade their facilities to offer multipurpose cold storage services. The latter in particular has been evolving rapidly from traditional go downs to modern facilities. Indian logistics market is expected to grow at a CAGR of 12.17% by 2020 driven by the growth in the manufacturing, retail, FMCG and e-commerce sectors. Indian cold storage market is expected to grow at a CAGR of 16.09% by 2020 driven by the growth in the organized retail, Indian fast food market, and food processing industry and e-commerce sectors. This facilitates the development of new technologies and ensures a high quality product. 4 Star Hotel Hotel is an establishment that provides lodging and usually meals and other services for travelers and other paying guests. It provides paid lodging, usually on a short-term basis. Hotels often provide a number of additional guest services such as a restaurant, laundry, a swimming pool or childcare. 4 Star Hotel is a hotel that provides above average, deluxe service and experience for the guest. First Class 4 Star hotel has a larger range of facilities available and the design is high quality. All service standards are aimed towards pleasing the guest. These hotels are usually located near city centers and are equipped with dining areas, exclusive facilities such as in-house gyms and swimming pools. The hotel industry in India is going through an interesting phase. One of the major reasons for the increase in demand for hotel rooms in the country is the boom in the overall Economy and high growth in sectors like information technology, telecom, retail and real estate. Rising stock market and new business opportunities are also attracting hordes of foreign investors and international corporate travelers to look for business opportunities in the country. The global hotels market was valued at approximately USD 147.57 billion in 2018 and is expected to generate around USD 211.54 billion by 2026, at a CAGR of around 4.6% between 2019 and 2026. The growing hospitality industry has resulted in the rising number of restaurants and hotels, which is expected to hotels market growth. The development of the travel and tourism industry has played a major role in the development of the hospitality industry and the hotels market. People travel from one place to another for various reasons, such as business trips, visits to relatives and friends, pilgrimages, for recreation and educational purposes, and to get access to quality healthcare facilities. Food and accommodation for people are taken care of by the hospitality industry. Hence, hospitality and tourism services are dependent on each other which, in turn, are expected to drive the hotels market growth. Aluminium Extrusion Aluminum extrusion is a technique used to transform aluminum alloy into objects with a definitive cross-sectional profile for a wide range of uses. The extrusion process makes the most of aluminum's unique combination of physical characteristics. Aluminium is a versatile material integral to modern life. The metal is found in everything from soda cans to cell phones to window frames to airplanes. The aluminium industry can be categorized into two principal segments. The key segment is the production of primary aluminium by integrated producers engaged in the entire value chain from the mining of bauxite in an alumina refinery and conversion of alumina into primary aluminium metal in an aluminium smelter. The global aluminum extrusion market was worth 19.1 Million Metric Tons in 2018. The market is reach a volume of 24.3 Million Metric Tons by 2024, CAGR of around 4% during 2019-2024. The demand for lightweight and high-performance materials such as aluminum, carbon fiber, and composites is increasing in automobile and aerospace and defense industries. Aluminum extruded products are used in the automotive industry to reduce emissions and improve the fuel efficiency of vehicles. Also, the high temperature and thermal shock resistance attributes of aluminum extruded products make them ideal for use in high-performance vehicles and high-performance engine applications. Moreover, aluminum extruded products have a high recycling rate and exhibit excellent creep resistance, fatigue resistance, and corrosion resistance. Thus the growing preference for lightweight and high-performance materials is one of the key aluminum extrusion market growth drivers. Increasing use of aluminum in electric and electric hybrid vehicles, rising complex structures in vehicles along with growing demand for high strength material are the key factors boosting the market growth. However, high production cost are restricting market growth. Dairy Farming & Dairy Products (Pasteurized Milk & Curd) The importance of milk in human diet especially for children and expectant and nursing matters is vital. To meet the demand of the increasing population milk production in India has to be increased. It is neither possible nor desirable to increase the cattle and buffalo population to achieve this target. This can only be achieved by stepping up milk production of our bovine population by cross breeding of cows and use of improved cows and cow. In India dairying has been practiced as a rural cottage industry since the remote past. Semi commercial dairying started with the establishment of military dairy farms and cooperative milk unions throughout the country towards the end of the Nineteenth century. Dairy products are generally defined as food products that are produced from milk. They are rich sources of energy. Raw milk for processing generally comes from cows, but occasionally from other mammals such as goats, sheep, and water buffalo. Water is the main constituent of milk (about 90%). Milk is a naturally nutrient rich and affordable product with a high nutrient to energy ratio. Milk and dairy products are an important food group in many national dietary guidelines and may play a role in dietary quality. The market is further expected to reach a value of INR 1,809.3 Billion by 2024 this is attributed to the nutritional benefits offered by plant-based dairy alternatives. They offer various nutritional benefits such as reduced cholesterol level, improved cardiovascular health, and diabetes control. These benefits have led to an increase in their consumption. Thus, these alternatives are catering to the demand for various dairy alternative products among global consumers. Tags #Cold_Storage_Project_Report, #Cold_Storage_and_Cold_Chain_Business, #Cold_Storage_Business_Project_Plan, #How_to_start_Cold_Storage_and_Cold_Chained_Business_in_India, #Huge_Subsidy-on_Cold_storage_projects, #Production_Of_I._V._Fluids, #IV_Fluid_Manufacturing_Plant, #Download_Iv_Fluids_Manufacturing_Process_Project_Report_Pdf, #Iv_Fluids_Manufacturing_Process_ppt, #Precipitated_Silica_from_Rice_Husk_Ash, Silica From Rice Husk Ash - Manufacturing Plant, Precipitated Silica From Rice Husk Ash in Project Reports, Project Report on Extraction Precipitated Silica Rice Husk Ash, precipitated silica from rice husk project report, rice husk ash silica manufacturer, rice husk ash business, project report on silica from rice husk, how to get silica from rice husk ash, silica from rice husk ash plant, rice husk ash silica manufacturer in India , Production Of Soft Gelatin Capsules (soft gel Capsules), Soft Gelatin Capsules in Project Reports & Profiles, Gelatin Capsule Manufacturing, Production of Soft Gelatin Capsules, manufacturing of soft gelatin capsule slide share, soft gelatin capsules, 4 Star Hotel -detailed Project Report, How to Start a Hotel Detailed Project Report?, Project report of 4 star hotel pdf, Report on new Business plan to set up a 7 star hotels, (PDF) Business Plan - Hotel Beach Resort, Aluminium Extrusion - Manufacturing Plant, Aluminium Extrusion Plant, business plan for aluminium plant, aluminium extrusion project report pdf, aluminium extrusion plant project report pdf, aluminium extrusion plant cost in India, aluminium extrusion plant layout, aluminium extrusion plant consultants, aluminium extrusion plant project cost, aluminium extrusion project report India, Dairy Farming & Dairy Products, How to Start Dairy & Milk Processing Industry, Project Profile On Dairy Products, Milk Project (Business Plan) , project report on dairy products pdf, dairy farming business plan pdf , project report on milk and milk products pdf, dairy farm business plan pdf India, milk powder business plan, dairy farming business plan ppt, dairy product business plan , Business Plan For Dairy Cow, Project Report on Milk Processing Plant, How to Start Agricultural Warehouse with Cold Storage Processing Industry in India, I.V. Fluids (BFS Technology) Processing Industry in India, Most Profitable Precipitated Silica from Rice Husk Ash Processing Business Ideas, Precipitated Silica from Rice Husk Ash Processing Projects, Small Scale Soft Gelatin Capsules Processing Projects, Starting a 4 Star Hotel Processing Business, How to Start a 4 Star Hotel Production Business, Aluminium Extrusion Based Small Scale Industries Projects, new small scale ideas in Dairy Farming & Dairy Products (Pasteurized Milk & Curd) processing industry
Plant capacity | Plant & machinery | Working capital | Cost of Project | T.C.I | Return | Break even |
---|---|---|---|---|---|---|
- | - | - | - | 1.00% | 0.00% |
Introduction
We can provide you detailed project reports on the following topics. Please select the projects of your interests.
Each detailed project reports cover all the aspects of business, from analysing the market, confirming availability of various necessities such as plant & machinery, raw materials to forecasting the financial requirements. The scope of the report includes assessing market potential, negotiating with collaborators, investment decision making, corporate diversification planning etc. in a very planned manner by formulating detailed manufacturing techniques and forecasting financial aspects by estimating the cost of raw material, formulating the cash flow statement, projecting the balance sheet etc.
We also offer self-contained Pre-Investment and Pre-Feasibility Studies, Market Surveys and Studies, Preparation of Techno-Economic Feasibility Reports, Identification and Selection of Plant and Machinery, Manufacturing Process and or Equipment required, General Guidance, Technical and Commercial Counseling for setting up new industrial projects on the following topics.
Many of the engineers, project consultant & industrial consultancy firms in India and worldwide use our project reports as one of the input in doing their analysis.
- One Lac / Lakh / Lakhs is equivalent to one hundred thousand (100,000)
- One Crore is equivalent to ten million (10,000,000)
- T.C.I is Total Capital Investment
- We can modify the project capacity and project cost as per your requirement.
- We can also prepare project report on any subject as per your requirement.
- Caution: The project's cost, capacity and return are subject to change without any notice. Future projects may have different values of project cost, capacity or return.
COST OF PROJECT | MEANS OF FINANCE | ||||||
---|---|---|---|---|---|---|---|
Particulars | Existing | Proposed | Total | Particulars | Existing | Proposed | Total |
Land & Site Development Exp. | ********** | ********** | ********** | Capital | ********** | ********** | ********** |
Buildings | ********** | ********** | ********** | Share Premium | ********** | ********** | ********** |
Plant & Machineries | ********** | ********** | ********** | Other Type Share Capital | ********** | ********** | ********** |
Motor Vehicles | ********** | ********** | ********** | Reserves & Surplus | ********** | ********** | ********** |
Office Automation Equipments | ********** | ********** | ********** | Cash Subsidy | ********** | ********** | ********** |
Technical Knowhow Fees & Exp. | ********** | ********** | ********** | Internal Cash Accruals | ********** | ********** | ********** |
Franchise & Other Deposits | ********** | ********** | ********** | Long/Medium Term Borrowings | ********** | ********** | ********** |
Preliminary & Pre-operative Exp | ********** | ********** | ********** | Debentures / Bonds | ********** | ********** | ********** |
Provision for Contingencies | ********** | ********** | ********** | Unsecured Loans/Deposits | ********** | ********** | ********** |
Margin Money - Working Capital | ********** | ********** | ********** | ********** | ********** | ********** | ********** |
Total | ********** | ********** | ********** | Total | ********** | ********** | ********** |
PARTICULARS | OPERATING YEARS | ||||
---|---|---|---|---|---|
1-2 | 2-3 | 3-4 | 4-5 | 5-6 | |
********** | ********** | ********** | ********** | ********** | |
Revenue/Income/Realisation | ********** | ********** | ********** | ********** | ********** |
Gross Sales Realisation | ********** | ********** | ********** | ********** | ********** |
Less : Excise Duties/Levies | ********** | ********** | ********** | ********** | ********** |
Net Sales Realisation | ********** | ********** | ********** | ********** | ********** |
Total Revenue/Income/Realisation | ********** | ********** | ********** | ********** | ********** |
********** | ********** | ********** | ********** | ********** | |
Expenses/Cost of Products/Services/Items | ********** | ********** | ********** | ********** | ********** |
Raw Material Cost | ********** | ********** | ********** | ********** | ********** |
Indigenous | ********** | ********** | ********** | ********** | ********** |
Total Nett Consumption | ********** | ********** | ********** | ********** | ********** |
Lab & ETP Chemical Cost | ********** | ********** | ********** | ********** | ********** |
Packing Material Cost | ********** | ********** | ********** | ********** | ********** |
Sub Total of Net Consumption | ********** | ********** | ********** | ********** | ********** |
Miscellaneous Cost | ********** | ********** | ********** | ********** | ********** |
Employees Expenses | ********** | ********** | ********** | ********** | ********** |
Fuel Expenses | ********** | ********** | ********** | ********** | ********** |
Power/Electricity Expenses | ********** | ********** | ********** | ********** | ********** |
Depreciation | ********** | ********** | ********** | ********** | ********** |
Royalty & Other Charges | ********** | ********** | ********** | ********** | ********** |
Repairs & Maintenance Exp. | ********** | ********** | ********** | ********** | ********** |
Other Mfg. Expenses | ********** | ********** | ********** | ********** | ********** |
Cost of Output of Goods Sold | ********** | ********** | ********** | ********** | ********** |
********** | ********** | ********** | ********** | ********** | |
Gross Profit | ********** | ********** | ********** | ********** | ********** |
Administration Expenses | ********** | ********** | ********** | ********** | ********** |
Technical Knowhow Fees & Exp. | ********** | ********** | ********** | ********** | ********** |
Financial Charges | ********** | ********** | ********** | ********** | ********** |
Long/Medium Term Borrowing | ********** | ********** | ********** | ********** | ********** |
On Wkg. Capital Borrowings | ********** | ********** | ********** | ********** | ********** |
Total Financial Charges | ********** | ********** | ********** | ********** | ********** |
Selling Expenses | ********** | ********** | ********** | ********** | ********** |
Total Cost of Sales | ********** | ********** | ********** | ********** | ********** |
********** | ********** | ********** | ********** | ********** | |
Net Profit Before Taxes | ********** | ********** | ********** | ********** | ********** |
Tax on Profit | ********** | ********** | ********** | ********** | ********** |
Net Profit After Taxes | ********** | ********** | ********** | ********** | ********** |
Depreciation Added Back | ********** | ********** | ********** | ********** | ********** |
Technical Knowhow Fees & Exp. | ********** | ********** | ********** | ********** | ********** |
Net Cash Accruals | ********** | ********** | ********** | ********** | ********** |
PARTICULARS | EXISTING | PROPOSED | TOTAL |
---|---|---|---|
COST OF PROJECT | |||
Land & Site Development Exp. | |||
Land Area Required | ********** | ********** | ********** |
Land Development Cost, Boundary Wall, Gate & Road etc. | ********** | ********** | ********** |
********** | ********** | ********** | |
Buildings | ********** | ********** | ********** |
Factory Building - | ********** | ********** | ********** |
Office Buildings | ********** | ********** | ********** |
********** | ********** | ********** | |
Plant & Machineries | ********** | ********** | ********** |
Indigenous Machineries | ********** | ********** | ********** |
Erection & Installation | ********** | ********** | ********** |
Laboratory Equipments | ********** | ********** | ********** |
Miscellaneous Equipments like pumps, valves, pipeline & fittings | ********** | ********** | ********** |
Imported Machineries | ********** | ********** | ********** |
Technical know how | ********** | ********** | ********** |
********** | ********** | ********** | |
Office Vehicles | ********** | ********** | ********** |
Office Automation Equipments (Telephone/ Fax/ Computer) | ********** | ********** | ********** |
Office Equipment, Furniture plus Other Equipment & Accessories | ********** | ********** | ********** |
Other Misc. Assets | ********** | ********** | ********** |
********** | ********** | ********** | |
Pre-operative & Preliminary Expenses | ********** | ********** | ********** |
Provision for Contingencies | ********** | ********** | ********** |
********** | ********** | ********** | |
Total Capital Cost of Project | ********** | ********** | ********** |
Margin Money for Working Capital | ********** | ********** | ********** |
Total Cost of Project | ********** | ********** | ********** |
PARTICULARS | STK.PRD. | STK.PRD. | OPERATING YEARS | |||||
---|---|---|---|---|---|---|---|---|
1st Year | 2nd Yr &+ | 1-2 | 2-3 | 3-4 | 4-5 | 5-6 | ||
Capacity | Months | Months | % | ********** | ********** | ********** | ********** | ********** |
CURRENT ASSETS | ********** | ********** | ********** | ********** | ********** | |||
Stocks on Hand | ********** | ********** | ********** | ********** | ********** | |||
Raw Material Cost | ********** | ********** | ********** | ********** | ********** | |||
Indigenous | ********** | ********** | M | ********** | ********** | ********** | ********** | ********** |
Lab & ETP Chemical | ********** | ********** | M | ********** | ********** | ********** | ********** | ********** |
Packing Material | ********** | ********** | M | ********** | ********** | ********** | ********** | ********** |
Consumable Store | ********** | ********** | M | ********** | ********** | ********** | ********** | ********** |
Work-in-Process | ********** | ********** | D | ********** | ********** | ********** | ********** | ********** |
Finished Goods | ********** | ********** | M | ********** | ********** | ********** | ********** | ********** |
Current Expenses | ********** | ********** | M | ********** | ********** | ********** | ********** | ********** |
Receivables | ********** | ********** | M | ********** | ********** | ********** | ********** | ********** |
********** | ********** | ********** | ********** | ********** | ********** | ********** | ||
Total | ********** | ********** | ********** | ********** | ********** | |||
Cash/Bank Balances | ********** | ********** | ********** | ********** | ********** | |||
Gross Wkg. Capital | ********** | ********** | ********** | ********** | ********** |
PARTICULARS | OPERATING YEARS | |||||
---|---|---|---|---|---|---|
1-2 | 2-3 | 3-4 | 4-5 | 5-6 | ||
Profit Percentages to Net Sales | ||||||
Gross Profit | ********** | ********** | ********** | ********** | ********** | |
% Of G.P. to Net Sales | ********** | ********** | ********** | ********** | ********** | |
Net Profit Before Taxes | ********** | ********** | ********** | ********** | ********** | |
% of N.P.B.T. To Net Sales | ********** | ********** | ********** | ********** | ********** | |
Net Profit After Taxes | ********** | ********** | ********** | ********** | ********** | |
% of N.P.A.T. To Net Sales | ********** | ********** | ********** | ********** | ********** | |
Debt Service Coverage Ratio | ********** | ********** | ********** | ********** | ********** | |
Debt Service Coverage Ratio | ||||||
Funds Available to Service Debts | ||||||
Net Profit After Taxes | ********** | ********** | ********** | ********** | ********** | |
Depreciation Charges | ********** | ********** | ********** | ********** | ********** | |
Technical Knowhow Fees & Exp | ********** | ********** | ********** | ********** | ********** | |
Interest on Long/Medium Term | ********** | ********** | ********** | ********** | ********** | |
Total | ********** | ********** | ********** | ********** | ********** | |
Debt Service Obligations | ||||||
Repayment of Long/Medium Term | ********** | ********** | ********** | ********** | ********** | |
Interest on Long/Medium Term | ********** | ********** | ********** | ********** | ********** | |
Total | ********** | ********** | ********** | ********** | ********** | |
********** | ********** | ********** | ********** | ********** | ||
D. S. C. R. (Individual) | ********** | ********** | ********** | ********** | ********** | |
D. S. C. R. (Cumulative) | ********** | ********** | ********** | ********** | ********** | |
D. S. C. R. (Overall) | ********** | ********** | ********** | ********** | ********** | |
Parameters | ||||||
Initial Equity Capital | ********** | ********** | ********** | ********** | ********** | ********** |
Credit Balance in P & L | ********** | ********** | ********** | ********** | ********** | ********** |
Total Capital exclUnsec Deposits | ********** | ********** | ********** | ********** | ********** | ********** |
Unsecured Dep. | ********** | ********** | ********** | ********** | ********** | ********** |
Total Equity incl Unsecured Deposits | ********** | ********** | ********** | ********** | ********** | ********** |
Long/Medium Term Borrowings from Bank | ********** | ********** | ********** | ********** | ********** | ********** |
Term lia. Incl Unsecured Deposit | ********** | ********** | ********** | ********** | ********** | ********** |
Total Liabilities | ********** | ********** | ********** | ********** | ********** | ********** |
Total Liabilities incl Unsecured Deposits | ********** | ********** | ********** | ********** | ********** | ********** |
DEBT EQUITY RATIO considering | ********** | ********** | ********** | ********** | ********** | ********** |
DEBT EQUITY RATIO considering | ||||||
I.E.Total Term Lia./NW | ||||||
Unsecured Dep. as Equity | ********** | ********** | ********** | ********** | ********** | ********** |
Unsecured Dep. as Debt | ********** | ********** | ********** | ********** | ********** | ********** |
Total Outside Lia./NW | ********** | ********** | ********** | ********** | ********** | ********** |
Total Outside Lia./NW | ********** | ********** | ********** | ********** | ********** | |
Assets Turnover Ratio (x) | ********** | ********** | ********** | ********** | ********** | |
No. of Shares of 10.00 each | ********** | ********** | ********** | ********** | ********** | |
Earnings Per Share (EPS) (in) | ********** | ********** | ********** | ********** | ********** | |
Proposed divident | ********** | ********** | ********** | ********** | ********** | |
Cash EPS (in) | ********** | ********** | ********** | ********** | ********** | |
Dividend Per Share(DPS) (in) | ********** | ********** | ********** | ********** | ********** | |
Payout Ratio (%Age) | ********** | ********** | ********** | ********** | ********** | |
Retained Earnings/Share (in) | ********** | ********** | ********** | ********** | ********** | |
Retained Earnings (%Age) | ********** | ********** | ********** | ********** | ********** | |
Book Value Per Share (in) | ********** | ********** | ********** | ********** | ********** | |
Debt Per Share (in) | ********** | ********** | ********** | ********** | ********** | |
Probable Mkt. Price/Share(in) | ********** | ********** | ********** | ********** | ********** | |
Price / Book Value (x) | ********** | ********** | ********** | ********** | ********** | |
Price Earnings Ratio (x) | ********** | ********** | ********** | ********** | ********** | |
Yield (%Age) | ********** | ********** | ********** | ********** | ********** |
PARTICULARS | OPERATING YEARS | |||||
---|---|---|---|---|---|---|
Ratio | 1-2 | 2-3 | 3-4 | 4-5 | 5-6 | |
BREAK EVEN ANALYSIS | ||||||
Total Value of Output | ********** | ********** | ********** | ********** | ********** | |
Variable Cost & Expenses | ||||||
Raw Material Cost | ********** | ********** | ********** | ********** | ********** | ********** |
Lab & ETP Chemical Cost | ********** | ********** | ********** | ********** | ********** | ********** |
Packing Material Cost | ********** | ********** | ********** | ********** | ********** | ********** |
Sales Commission/Exp. | ********** | ********** | ********** | ********** | ********** | ********** |
Sub-total | ********** | ********** | ********** | ********** | ********** | |
Less: W.I.P. Adjustments | ********** | ********** | ********** | ********** | ********** | |
Total Variable Cost | ********** | ********** | ********** | ********** | ********** | |
Net Contribution | ********** | ********** | ********** | ********** | ********** | |
Profit Volume Ratio (%) | ********** | ********** | ********** | ********** | ********** | |
Semi-Var./Semi-Fixed Exp. | ********** | ********** | ********** | ********** | ********** | ********** |
Miscellaneous Cost | ********** | ********** | ********** | ********** | ********** | ********** |
Employees Expenses | ********** | ********** | ********** | ********** | ********** | ********** |
Power/Electricity Expen | ********** | ********** | ********** | ********** | ********** | ********** |
Fuel Expenses | ********** | ********** | ********** | ********** | ********** | ********** |
Royalty & Other Charges | ********** | ********** | ********** | ********** | ********** | ********** |
Repairs & Maintenance E | ********** | ********** | ********** | ********** | ********** | ********** |
Other Mfg. Expenses | ********** | ********** | ********** | ********** | ********** | ********** |
Administration Expenses | ********** | ********** | ********** | ********** | ********** | ********** |
Selling Expenses | ********** | ********** | ********** | ********** | ********** | ********** |
Interest on Wkg.Capital | ********** | ********** | ********** | ********** | ********** | ********** |
Tot.Semi-Var./Fixed Exp. | ********** | ********** | ********** | ********** | ********** | ********** |
Fixed Expenses / Cost | ********** | ********** | ********** | ********** | ********** | ********** |
Miscellaneous Cost | ********** | ********** | ********** | ********** | ********** | ********** |
Employees Expenses | ********** | ********** | ********** | ********** | ********** | ********** |
Power/Electricity Expen | ********** | ********** | ********** | ********** | ********** | ********** |
Fuel Expenses | ********** | ********** | ********** | ********** | ********** | ********** |
Royalty & Other Charges | ********** | ********** | ********** | ********** | ********** | ********** |
Repairs & Maintenance E | ********** | ********** | ********** | ********** | ********** | ********** |
Other Mfg. Expenses | ********** | ********** | ********** | ********** | ********** | ********** |
Administration Expenses | ********** | ********** | ********** | ********** | ********** | ********** |
Selling Expenses | ********** | ********** | ********** | ********** | ********** | ********** |
Intrest-Fixed Borrowing | ********** | ********** | ********** | ********** | ********** | ********** |
Intrest-Working Capital | ********** | ********** | ********** | ********** | ********** | ********** |
Depreciation Charges | ********** | ********** | ********** | ********** | ********** | ********** |
Deferred Expenses W/Off | ********** | ********** | ********** | ********** | ********** | ********** |
Total Fixed Expenses | ********** | ********** | ********** | ********** | ********** | ********** |
Tot.Fixed/Semi-Fixed Exp | ********** | ********** | ********** | ********** | ********** | ********** |
Tot.Cash Fixed/SemiFixed | ********** | ********** | ********** | ********** | ********** | ********** |
Cash Break Even Sales | ********** | ********** | ********** | ********** | ********** | ********** |
Cash Margin of Safety | ********** | ********** | ********** | ********** | ********** | ********** |
Break Even Sales | ********** | ********** | ********** | ********** | ********** | ********** |
Margin of safety | ********** | ********** | ********** | ********** | ********** | ********** |
At Maximum Utilisation : | Year | ********** | ********** | ********** | ********** | ********** |
(as % of Installed Capacity) | ||||||
Cash B.E.P. : | % | xx% | xx% | xx% | xx% | xx% |
B.E.P. : | % | xx% | xx% | xx% | xx% | xx% |
MEANS OF FINANCE | |||
---|---|---|---|
Equity Share Capital | ********** | ********** | ********** |
Others - Preference Share Capital | ********** | ********** | ********** |
Total Equity Share Capital | ********** | ********** | ********** |
********** | ********** | ********** | |
Long/Medium Term Borrowings | ********** | ********** | ********** |
FROM BANK | ********** | ********** | ********** |
From Other Financial Institutions | ********** | ********** | ********** |
Total Long/Medium Term Borrowings | ********** | ********** | ********** |
********** | ********** | ********** | |
Total Means of Finance | ********** | ********** | ********** |
PARTICULARS | OPERATING YEARS | ||||
---|---|---|---|---|---|
1-2 | 2-3 | 3-4 | 4-5 | 5-6 | |
Equity Share Capital | ********** | ********** | ********** | ********** | ********** |
Surplus of Previous Year | ********** | ********** | ********** | ********** | ********** |
Add : Net Profit After Taxes | ********** | ********** | ********** | ********** | ********** |
Surplus at the End of Year | ********** | ********** | ********** | ********** | ********** |
Unsecured Deposits | ********** | ********** | ********** | ********** | ********** |
Long/Medium Term Borrowings Proposed-FROM BANK | ********** | ********** | ********** | ********** | ********** |
Bank Borrowing for Wkg. Capital | ********** | ********** | ********** | ********** | ********** |
Current Liabilities | ********** | ********** | ********** | ********** | ********** |
Sundry Creditors | ********** | ********** | ********** | ********** | ********** |
Other Current Liabilities | ********** | ********** | ********** | ********** | ********** |
Total Current Liabilities | ********** | ********** | ********** | ********** | ********** |
********** | ********** | ********** | ********** | ********** | |
Total of Liabilities | ********** | ********** | ********** | ********** | ********** |
********** | ********** | ********** | ********** | ********** | |
ASSETS | ********** | ********** | ********** | ********** | ********** |
Fixed Assets | ********** | ********** | ********** | ********** | ********** |
Gross Block | ********** | ********** | ********** | ********** | ********** |
Less : Depreciation to Date | ********** | ********** | ********** | ********** | ********** |
Net Block | ********** | ********** | ********** | ********** | ********** |
Current Assets | ********** | ********** | ********** | ********** | ********** |
Stocks on Hand | ********** | ********** | ********** | ********** | ********** |
Receivables | ********** | ********** | ********** | ********** | ********** |
Other Current Assets | ********** | ********** | ********** | ********** | ********** |
Cash and Bank Balances | ********** | ********** | ********** | ********** | ********** |
Total Current Assets | ********** | ********** | ********** | ********** | ********** |
P & P Exp. and/or Other Dvp.Exp. | ********** | ********** | ********** | ********** | ********** |
(To The Extent Not W/Off) | ********** | ********** | ********** | ********** | ********** |
Other Non Current Assets | ********** | ********** | ********** | ********** | ********** |
********** | ********** | ********** | ********** | ********** | |
Total of Assets | ********** | ********** | ********** | ********** | ********** |
ROI (Average of Fixed Assets) | ********** | ********** | ********** | ********** | ********** |
RONW (Average of Share Capital) | ********** | ********** | ********** | ********** | ********** |
ROI (Average of Total Assets) | ********** | ********** | ********** | ********** | ********** |
INTEREST AND REPAYMENT ON TERM LOANS
A | Name of Institution-Bank | ABC BANK | |
---|---|---|---|
B | Term Borrowing Amount | ********** | xx |
C | Repayment Term (Years) | ********** | Years |
D | Repayment Instalments | ********** | Instalments |
E | Repayment Commencement | Year - 0; 3rd Qtr. | |
F | Rate of Interest(General) | xxxx% | p.a. |
G | Rate of Interest(Initial) | 0.00% | p.a. |
H | Apply Gen. Int. Rate from Year | x Quarter :: x | |
I | Interest Calculation | Quarterly |
Debt Service Coverage Ratio | ||||||
---|---|---|---|---|---|---|
Funds Available to Service Debts | ||||||
Net Profit After Taxes | ********** | ********** | ********** | ********** | ********** | |
Depreciation Charges | ********** | ********** | ********** | ********** | ********** | |
Technical Knowhow Fees & Expenses | ********** | ********** | ********** | ********** | ********** | |
Interest on Long/Medium Term | ********** | ********** | ********** | ********** | ********** | |
Total | ********** | ********** | ********** | ********** | ********** | |
Debt Service Obligations | ********** | ********** | ********** | ********** | ********** | |
Repayment of Long/Medium Term | ********** | ********** | ********** | ********** | ********** | |
Interest on Long/Medium Term | ********** | ********** | ********** | ********** | ********** | |
Total | ********** | ********** | ********** | ********** | ********** | |
********** | ********** | ********** | ********** | ********** | ||
D. S. C. R. (Individual) | ********** | ********** | ********** | ********** | ********** | |
D. S. C. R. (Cumulative) ..... | ********** | ********** | ********** | ********** | ********** | |
D. S. C. R. (Overall) ........ | ********** | ********** | ********** | ********** | ********** |
DEPRECIATION CHARGES AS PER BOOKS (TOTAL)
Operating Year | F.Assets Type A-1 | F.Assets Type A-2 | F.Assets Type B | F.Assets Type C | F.Assets Type D-1 | F.Assets Type D-2 | Total |
---|---|---|---|---|---|---|---|
Particulars | Factory Building | Office Buildings | Plant & Machinery | Office Vehicles | Office Automation Equipments (Telephone/ Fax/ Computer) | Furniture & Fixtures | |
1-2 | ********** | ********** | ********** | ********** | ********** | ********** | ********** |
********** | ********** | ********** | ********** | ********** | ********** | ********** | |
********** | ********** | ********** | ********** | ********** | ********** | ********** | |
2-3 | ********** | ********** | ********** | ********** | ********** | ********** | ********** |
********** | ********** | ********** | ********** | ********** | ********** | ********** | |
********** | ********** | ********** | ********** | ********** | ********** | ********** | |
3-4 | ********** | ********** | ********** | ********** | ********** | ********** | ********** |
********** | ********** | ********** | ********** | ********** | ********** | ********** | |
********** | ********** | ********** | ********** | ********** | ********** | ********** | |
4-5 | ********** | ********** | ********** | ********** | ********** | ********** | ********** |
********** | ********** | ********** | ********** | ********** | ********** | ********** | |
********** | ********** | ********** | ********** | ********** | ********** | ********** | |
5-6 | ********** | ********** | ********** | ********** | ********** | ********** | ********** |
********** | ********** | ********** | ********** | ********** | ********** | ********** | |
********** | ********** | ********** | ********** | ********** | ********** | ********** |
Particulars | Method | Deprn.Rate | Part Consideration (for Asset put to use less than xx months) |
---|---|---|---|
Type A :: Buildings | |||
Factory Building - | WDV | ********** | ********** |
Office Buildings | WDV | ********** | ********** |
Type C | |||
Office Vehicles | WDV | ********** | ********** |
Type D :: Misc. Fixed Assets | |||
Office Automation Equipments (Telephone/ Fax/ Computer) | WDV | ********** | ********** |
Furniture & Fixtures | WDV | ********** | ********** |
Type B :: Plant & Machineries |
Projected Pay Back Period | |||||
---|---|---|---|---|---|
Particulars | Operating Years | ||||
1-2 | 2-3 | 3-4 | 4-5 | 5-6 | |
Year | 1 | 2 | 3 | 4 | 5 |
Initial Investment | ********* | ||||
Total Initial Investment | ********* | ||||
Yearly Cash Flow | ********* | ********* | ********* | ********* | ********* |
Accumulated Cash Flow | ********* | ********* | ********* | ********* | ********* |
Accumulated Cash Flow | ********* | ********* | ********* | ********* | ********* |
Pay Back Period | xx Years xx Months | xx Years xx months |
Projected IRR | |||||
---|---|---|---|---|---|
Year | CFAT | PV factor @**% | ********* | ||
Initial Investment | ********* | ********* | ********* | ||
1-2 | ********* | ********* | ********* | ||
2-3 | ********* | ********* | ********* | ||
3-4 | ********* | ********* | ********* | ||
4-5 | ********* | ********* | ********* | ||
5-6 | ********* | ********* | ********* | ||
Total PV | ********* | ********* | |||
IRR | ********* | ********* | |||
NIIR PROJECT CONSULTANCY SERVICES (NPCS) is a reliable name in the industrial world for offering integrated technical consultancy services. NPCS is manned by engineers, planners, specialists, financial experts, economic analysts and design specialists with extensive experience in the related industries.
Our various services are: Detailed Project Report, Business Plan for Manufacturing Plant, Start-up Ideas, Business Ideas for Entrepreneurs, Start up Business Opportunities, entrepreneurship projects, Successful Business Plan, Industry Trends, Market Research, Manufacturing Process, Machinery, Raw Materials, project report, Cost and Revenue, Pre-feasibility study for Profitable Manufacturing Business, Project Identification, Project Feasibility and Market Study, Identification of Profitable Industrial Project Opportunities, Business Opportunities, Investment Opportunities for Most Profitable Business in India, Manufacturing Business Ideas, Preparation of Project Profile, Pre-Investment and Pre-Feasibility Study, Market Research Study, Preparation of Techno-Economic Feasibility Report, Identification and Selection of Plant, Process, Equipment, General Guidance, Startup Help, Technical and Commercial Counseling for setting up new industrial project and Most Profitable Small Scale Business.
NPCS also publishes varies process technology, technical, reference, self employment and startup books, directory, business and industry database, bankable detailed project report, market research report on various industries, small scale industry and profit making business. Besides being used by manufacturers, industrialists and entrepreneurs, our publications are also used by professionals including project engineers, information services bureau, consultants and project consultancy firms as one of the input in their research.
- This report helps you to identify a profitable project for investing or diversifying into by throwing light to crucial areas like industry size, demand of the product and reasons for investing in the product.
- This report provides vital information on the product like its definition, characteristics and segmentation.
- This report helps you market and place the product correctly by identifying the target customer group of the product.
- This report helps you understand the viability of the project by disclosing details like raw materials required, manufacturing process, project costs and snapshot of other project financials.
- The report provides forecasts of key parameters which helps to anticipate the industry performance and make sound business decision.
- Our research reports broadly cover Indian markets, present analysis, outlook and forecast.
- The market forecasts are developed on the basis of secondary research and are cross-validated through interactions with the industry players.
- We use reliable sources of information and databases. And information from such sources is processed by us and included in the report.
Introduction
- Project Introduction
- Project Objective and Strategy
- Concise History of the Product
- Properties
- BIS (Bureau of Indian Standards) Provision & Specification
- Uses & Applications
Market Study and Assessment
- Current Indian Market Scenario
- Present Market Demand and Supply
- Estimated Future Market Demand and Forecast
- Statistics of Import & Export
- Names & Addresses of Existing Units (Present Players)
- Market Opportunity
Raw Material
- List of Raw Materials
- Properties of Raw Materials
- Prescribed Quality of Raw Materials
- List of Suppliers and Manufacturers
Personnel (Manpower) Requirements
- Requirement of Staff & Labor (Skilled and Unskilled) Managerial, Technical, Office Staff and Marketing Personnel
Plant and Machinery
- List of Plant & Machinery
- Miscellaneous Items
- Appliances &Equipments
- Laboratory Equipments& Accessories
- Electrification
- Electric Load & Water
- Maintenance Cost
- Sources of Plant & Machinery (Suppliers and Manufacturers)
Manufacturing Process and Formulations
- Detailed Process of Manufacture with Formulation
- Packaging Required
- Process Flow Sheet Diagram
Infrastructure and Utilities
- Project Location
- Requirement of Land Area
- Rates of the Land
- Built Up Area
- Construction Schedule
- Plant Layout and Requirement of Utilities
- Assumptions for Profitability workings
- Plant Economics
- Production Schedule
-
- Land & Building
- Factory Land & Building
- Site Development Expenses
-
- Plant & Machinery
- Indigenous Machineries
- Other Machineries (Miscellaneous, Laboratory etc.)
-
- Other Fixed Assets
- Furniture & Fixtures
- Pre-operative and Preliminary Expenses
- Technical Knowhow
- Provision of Contingencies
-
- Working Capital Requirement Per Month
- Raw Material
- Packing Material
- Lab & ETP Chemical Cost
- Consumable Store
-
- Overheads Required Per Month And Per Annum
- Utilities & Overheads (Power, Water and Fuel Expenses etc.)
- Royalty and Other Charges
- Selling and Distribution Expenses
- Salary and Wages
- Turnover Per Annum
-
- Share Capital
- Equity Capital
- Preference Share Capital
- Annexure 1:: Cost of Project and Means of Finance
-
- Annexure 2:: Profitability and Net Cash Accruals
- Revenue/Income/Realisation
- Expenses/Cost of Products/Services/Items
- Gross Profit
- Financial Charges
- Total Cost of Sales
- Net Profit After Taxes
- Net Cash Accruals
-
- Annexure 3 :: Assessment of Working Capital requirements
- Current Assets
- Gross Working. Capital
- Current Liabilities
- Net Working Capital
- Working Note for Calculation of Work-in-process
- Annexure 4 :: Sources and Disposition of Funds
-
- Annexure 5 :: Projected Balance Sheets
- ROI (Average of Fixed Assets)
- RONW (Average of Share Capital)
- ROI (Average of Total Assets)
-
- Annexure 6 :: Profitability ratios
- D.S.C.R
- Earnings Per Share (EPS)
- Debt Equity Ratio
-
- Annexure 7 :: Break-Even Analysis
- Variable Cost & Expenses
- Semi-Var./Semi-Fixed Exp.
- Profit Volume Ratio (PVR)
- Fixed Expenses / Cost
- B.E.P
-
- Annexure 8 to 11:: Sensitivity Analysis-Price/Volume
- Resultant N.P.B.T
- Resultant D.S.C.R
- Resultant PV Ratio
- Resultant DER
- Resultant ROI
- Resultant BEP
-
- Annexure 12 :: Shareholding Pattern and Stake Status
- Equity Capital
- Preference Share Capital
-
- Annexure 13 :: Quantitative Details-Output/Sales/Stocks
- Determined Capacity P.A of Products/Services
- Achievable Efficiency/Yield % of Products/Services/Items
- Net Usable Load/Capacity of Products/Services/Items
- Expected Sales/ Revenue/ Income of Products/ Services/ Items
- Annexure 14 :: Product wise domestic Sales Realisation
- Annexure 15 :: Total Raw Material Cost
- Annexure 16 :: Raw Material Cost per unit
- Annexure 17 :: Total Lab & ETP Chemical Cost
- Annexure 18 :: Consumables, Store etc.,
- Annexure 19 :: Packing Material Cost
- Annexure 20 :: Packing Material Cost Per Unit
- Annexure 21 :: Employees Expenses
- Annexure 22 :: Fuel Expenses
- Annexure 23 :: Power/Electricity Expenses
- Annexure 24 :: Royalty & Other Charges
- Annexure 25 :: Repairs & Maintenance Exp.
- Annexure 26 :: Other Mfg. Expenses
- Annexure 27 :: Administration Expenses
- Annexure 28 :: Selling Expenses
- Annexure 29 :: Depreciation Charges – as per Books (Total)
- Annexure 30 :: Depreciation Charges – as per Books (P & M)
- Annexure 31 :: Depreciation Charges - As per IT Act WDV (Total)
- Annexure 32 :: Depreciation Charges - As per IT Act WDV (P & M)
- Annexure 33 :: Interest and Repayment - Term Loans
- Annexure 34 :: Tax on Profits
- Annexure 35 ::Projected Pay-Back Period And IRR
- One Lac / Lakh / Lakhs is equivalent to one hundred thousand (100,000)
- One Crore is equivalent to ten million (10,000,000)
- T.C.I is Total Capital Investment
- We can modify the project capacity and project cost as per your requirement.
- We can also prepare project report on any subject as per your requirement.
- Caution: The project's cost, capacity and return are subject to change without any notice. Future projects may have different values of project cost, capacity or return.
Need assistance?
Share your details, we will call you
NIIR PROJECT CONSULTANCY SERVICES (NPCS) is a reliable name in the industrial world for offering integrated technical consultancy services.
Read more →Quick Links
Products & Services
Contact Info
106-E, Kamla Nagar,
New Delhi-110007, India. |
|
+91 9097-075-054, +91-11-23843955, +91-11-23845886 Any quries? Call us. |
|
[email protected]
Any quries? Mail Now. |
- Copyright © 2000-2025 NPCS, All Right Reserved.
X
Have a business idea? Let’s make it
happen together-contact us now!